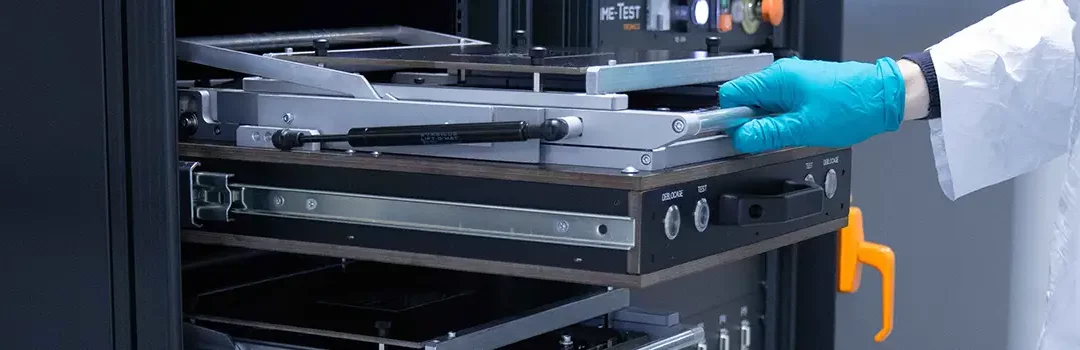
- The Testman's Corner
Test Strategy
We explain what needs to be done
Did you know? A well thought-out test strategy is essential!
A good test strategy sets up the roadmap for structural and functional testing by defining a vision, a schedule and a methodology, with the ultimate goal of verifying that the solution meets the customer’s needs.
Defining the optimal strategy involves trade-offs between:
- Operating costs
- Investment costs
- Coverage rates
- Test rates
- Diagnostic resolution
- Speed of process feedback
- Long-term product reliability
We can visualize it as such:
Failure Mode, Effects and Criticality Analyses (FMECA) are also essential inputs. The test strategy will be an important input for the Design For Test (DfT) analyses.
To develop a good test strategy, you use existing means (AOI, Rx, mobile probe tester, in-situ tester, boundary scan, etc.) to which you will probably need to add ad-hoc structural tests, functional tests, reliability tests (burn-in, vibration tests, etc.) and a final acceptance test sometimes meeting a certain standard (aeronautics, space, medical, etc.).
When to test and with which equipment?
There is no universal technique. Setting up a good test strategy requires a study that will bring real added value to your product and help you get the best out of your equipment.
A test strategy covers the following areas:
- Measuring the solution’s performance: indicators
- Analyzing the solution’s performance: campaigns, scenarios, cases and data sets for the whole series of tests
- Identifying the solution’s limits: technical and organizational areas
- Defining and applying corrective and evolutionary actions
When your test strategy is clearly defined, you can then use your equipment, acquire the equipment missing from your test flow chart and develop the resources to complement your needs.
Our unique offer helps you to find your way through the tests to be applied during the life of your products:
- Also in The Testman's Corner